Design Envelope technology is a demand based intelligent control solution that models equipment and system behavior, monitors actual system conditions, and dynamically adjusts equipment operation to match system demand. Design Envelope technology is at the core of Armstrong’s groundbreaking advances in building performance. Design Envelope technology enables the greenest, most flexible and most cost effective fluid-flow and HVAC systems on the planet – resulting in both, lowest installed and lowest operating cost with the same equipment.
Industry Leading Capabilities
Armstrong has reinvented and redesigned our pumping solutions to include connectivity and performance management services. Design Envelope solutions provide optimal lifetime efficiency and lowest cost. No other pumping solution offers the same expanded performance range, one touch commissioning, Sensorless speed control, flow monitoring accuracy and operating notifications.
Connectivity
Built-in Wi-Fi capability supports remote
control, real-time monitoring and
management for lowest operating costs
|
|
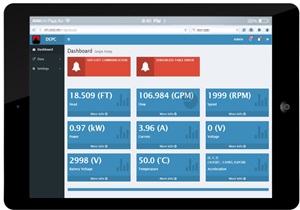
|
Local and remote access from
any smart device
|
|
Adaptive browser-compatible software
and intuitive user interface
|
|
Optimum Lifetime Performance
Design Envelope solutions offer up to 70% energy savings compared to standard industry pumps.
A breakdown of incremental and cumulative savings looks like this:
Configuration |
|
Power |
|
Energy savings |
|
Energy savings |
Constant Speed Throttled |
|
32.03 |
|
Incremental |
|
Cumulative |
Reduced Speed Unthrottled-Constant Flow |
|
27.11 |
|
15% |
|
15% |
Reduced Constant Speed-Variable Flow |
|
19.36 |
|
29% |
|
40% |
Variable Speed-Variable Flow Using Mechanical Room Sensor |
|
14.35 |
|
26% |
|
55% |
Integrated Sensorless Control |
|
7.32 |
|
49% |
|
77% |
In multi-pump installations, Armstrong's patented Parallel Sensorless Pump Control saves up to 30% more energy over industry-standard pump staging methodologies. Now, Armstrong's Intelligent Motor Technology, certified to IE5 standards and available on 1 to 10 hp models, delivers 3 – 12 % additional motor efficiency.
This adds up to pumping efficiency that is simply unmatched anywhere in the industry.
Control Capabilities
With the new advanced controller, offering extended intelligence and control options, Armstrong has advanced pumping technology well beyond the current standard. Control packages currently available with design envelope technology include:
performance
packages |
functions
included |
|
|
design envelope optimization |
Pump Manager is a performance management service to help operators maintain optimized long-term efficiency.
|
key stats |
30% of HVAC systems are not properly installed |
Another 30% are not properly commissioned. |
Regular commissioning of equipment prevents a 9% performance degradation |
Armstrong's optional Pump Manager service helps building owners and operators prevent degradation in HVAC efficiency. |
Maintain optimal long-term pump efficiency |
Maximize uptime |
Avoid catastrophic failures and disruption |
Avoid emergency repair costs
|
|
 |
Sensorless Bundle (standard) |
• Sensorless control
• Flow readout
• Constant flow
• Constant pressure |
 |
Parallel Sensorless
(standard on Tango
and dualARMs) |
Parallel Sensorless control |

|
Energy Performance
Bundle (requires
Sensorless Bundle) |
• Auto-flow balancing
• Maximum flow control |
 |
Protection Bundle (requires Sensorless Bundle) |
• Minimum Flow Control
• Bypass Valve Control
|
 |
Zone Optimization
|
• 2 Sensor Control
|
 |
Dual Season Setup
|
• Pre-set heating and cooling parameters for 2-pipe systems
|
Optimum life-time building performance
Pump Manager is a performance management service to help operators maintain optimized long-term efficiency.
Unmatched efficiency
- In the 1-10 HP range Design Envelope uses a completely new, fully-integrated design, where every element is optimized for overall performance. The new Armstrong iECMTM motor with integrated controls, delivers IE5 levels of efficiency.
- Tango pumps offer the pinnacle of energy performance and lifetime value with on-board Parallel Sensorless Pump ControlTM , enabling a completely new approach to system and component redundancy
Optimized lifetime performance through real-time insight and action
- Our full line of pump offerings, from 1 hp to 1250 HP, are all delivered with both wireless and wired connectivity, providing both on-site access to real-time performance and pump conditions as well as connectivity to support Pump Manager, an optional performance management monitoring and reporting service
- Real-time pump performance monitoring capability supports extended energy performance of each pump as well as notifications and recommendations based on pump conditions
- industry studies suggest that “as commissioned” HVAC performance can be extended through a program of monitoring and tuning, resulting in energy savings of 10 to 15%
design envelope automation |
Armstrong has re-invented and redesigned pumping solutions to include connectivity and performance management services. Design Envelope provides optimal lifetime efficiency through:
|
Expanded performance range
|
One-touch commissioning
|
Pump speed modulation based on an adjustable quadratic control curve for better
|
Part-load efficiency
|
Flow monitoring accuracy (+/- 5%)
|
Operating data and notifications to support diagnostics and service
|
No other pumping solution offers comparable features for automation, self-diagnosis, reporting and commissioning.